Choosing the Right Welding Method for Your Truck: MIG, TIG, Stick, and Beyond
Fix your truck right! MIG, TIG, Stick & other welding methods compared. Learn which is best for bodywork, frames, exhaust, fuel tanks & more. Discover pros & cons of each method (ease of use, precision, durability) to make informed choices for your truck repairs.
Welding plays a significant role in this maintenance, whether it’s for repairs, modifications, or fabrications. Understanding the different welding methods can help you choose the right technique for your needs. Here, we delve into four key welding methods: MIG, TIG, Stick, and advanced techniques.
If you require welding and fabrication near Cleburne, Texas, please visit our Welding and Fabrication Services page here.
MIG Welding: Versatility and Ease of Use
Overview
MIG (Metal Inert Gas) welding, also known as Gas Metal Arc Welding (GMAW), is one of the most popular welding methods due to its versatility and ease of use. It involves feeding a continuous solid wire electrode through a welding gun into the weld pool, joining the base materials together. A shielding gas, typically argon or a mixture of argon and carbon dioxide, protects the weld pool from contamination.
Applications in Truck Maintenance
MIG welding is ideal for various truck repair and maintenance tasks, particularly for bodywork and minor structural repairs. It excels in welding thinner metals commonly found in truck bodies, such as aluminum and mild steel.
- Bodywork Repairs: Ideal for fixing dents, cracks, and other damages on truck panels.
- Frame Repairs: Useful for welding truck frames and chassis when lighter gauge materials are involved.
- Accessory Fabrication: Excellent for creating custom accessories like toolboxes and brackets.
Advantages
MIG welding stands out for its simplicity, making it a preferred choice for both beginners and seasoned professionals.
- Ease of Use: The process is straightforward, with minimal setup and adjustments required.
- Continuous Wire Feed: Allows for consistent welds, reducing the risk of weld defects.
- High Welding Speed: Efficient for completing large projects quickly.
- Minimal Cleanup: Produces less spatter compared to other methods, resulting in cleaner welds.
Considerations
While MIG welding offers numerous benefits, there are some considerations to keep in mind.
- Shielding Gas Requirement: Not ideal for outdoor use where wind can disrupt the gas flow.
- Clean Environment Needed: The welding area must be free of contaminants to prevent weld defects.
TIG Welding: Precision and Quality
Overview
TIG (Tungsten Inert Gas) welding, also known as Gas Tungsten Arc Welding (GTAW), is renowned for its precision and high-quality welds. This method uses a non-consumable tungsten electrode to produce the weld. An inert gas, usually argon, shields the weld area from atmospheric contamination.
Applications in Truck Maintenance
TIG welding is essential for tasks that require precision and high-quality finishes, making it suitable for critical components in truck maintenance.
- Exhaust Systems: Ideal for welding thin materials and creating airtight seals in exhaust systems.
- Fuel Tanks: Ensures leak-proof joints in fuel tanks, which is crucial for safety.
- Aluminum Parts: Perfect for welding aluminum parts due to its control and precision.
Advantages
TIG welding offers unmatched control and precision, which are critical for certain truck maintenance tasks.
- Precision and Control: Allows for detailed work, producing clean and precise welds.
- Superior Weld Quality: Minimal spatter and cleanup required, resulting in aesthetically pleasing welds.
- Versatility: Can weld a wide range of metals, including aluminum, stainless steel, and magnesium.
Considerations
Despite its advantages, TIG welding comes with some challenges.
- Higher Skill Level Required: Requires more expertise compared to MIG welding.
- Slower Welding Speed: Not as fast as other methods, which can be a drawback for large projects.
- Clean Environment Needed: Similar to MIG welding, the workspace must be clean to prevent contamination.
Stick Welding: Durability and Versatility
Overview
Stick welding, also known as Shielded Metal Arc Welding (SMAW), is one of the oldest and most reliable welding methods. It uses a consumable electrode coated with flux to lay the weld. An electric current forms an arc between the electrode and the metals to be joined.
Applications in Truck Maintenance
Stick welding is highly effective for heavy-duty structural repairs and on-site maintenance.
- Structural Repairs: Ideal for welding truck frames and heavy-duty components.
- Outdoor Repairs: Suitable for use in adverse conditions, including wind and rain, making it perfect for field repairs.
- Thick Metal Components: Excels in welding thicker metals and creating strong joints.
Advantages
Stick welding is favored for its durability and versatility in various conditions.
- Durability: Produces strong and durable welds, essential for heavy-duty applications.
- Versatility: Capable of welding different metals and thicknesses.
- Cost-Effective: Requires minimal equipment, making it an economical choice.
- Portable: Equipment is easy to transport, suitable for fieldwork.
Considerations
Stick welding also has its set of challenges that need to be considered.
- Higher Skill Level Needed: Requires more experience and skill to produce quality welds.
- Slag Removal: Post-weld cleanup involves removing slag, which can be time-consuming.
- Slower Welding Speed: Generally slower than MIG welding, affecting productivity.
Beyond the Basics: Advanced Welding Techniques
Overview
Beyond the conventional methods, several advanced welding techniques offer specialized solutions for truck maintenance and customization.
Plasma Arc Welding (PAW)
Plasma Arc Welding (PAW) uses a plasma torch to generate a precise and stable arc. It is used in high-quality, intricate welds for custom truck modifications.
- Precision: Offers high precision, making it suitable for detailed work.
- High-Quality Welds: Produces clean and strong welds, ideal for custom modifications.
Flux-Cored Arc Welding (FCAW)
Similar to MIG welding, Flux-Cored Arc Welding (FCAW) uses a flux-cored wire, making it advantageous in specific scenarios.
- Outdoor Use: Effective in windy conditions due to the flux-cored wire that doesn't require an external shielding gas.
- Heavy-Duty Applications: Suitable for thicker materials and heavy-duty repairs.
Laser Welding
Laser welding employs a high-energy laser beam to join materials. It is often used in cutting-edge automotive and truck manufacturing.
- Precision: Provides unparalleled precision, suitable for delicate and high-strength welds.
- High Strength: Produces strong, reliable welds with minimal heat-affected zones.
Choosing the Right Method
Selecting the appropriate welding method depends on several factors, including the type of metal, material thickness, working environment, and the skill level of the welder.
- Metal Type and Thickness: Consider the metals involved and their thickness. MIG is good for thinner metals, TIG for precise work, and Stick for thicker, heavy-duty materials.
- Environment: Evaluate whether the work will be done indoors or outdoors. MIG and TIG require clean environments, while Stick and FCAW can handle outdoor conditions.
- Skill Level: Assess the skill level of the person performing the weld. MIG is beginner-friendly, while TIG and Stick require more expertise.
By understanding these factors, you can make an informed decision, ensuring that your truck maintenance and repairs are performed with the highest standards of quality and efficiency.
More Industry Articles
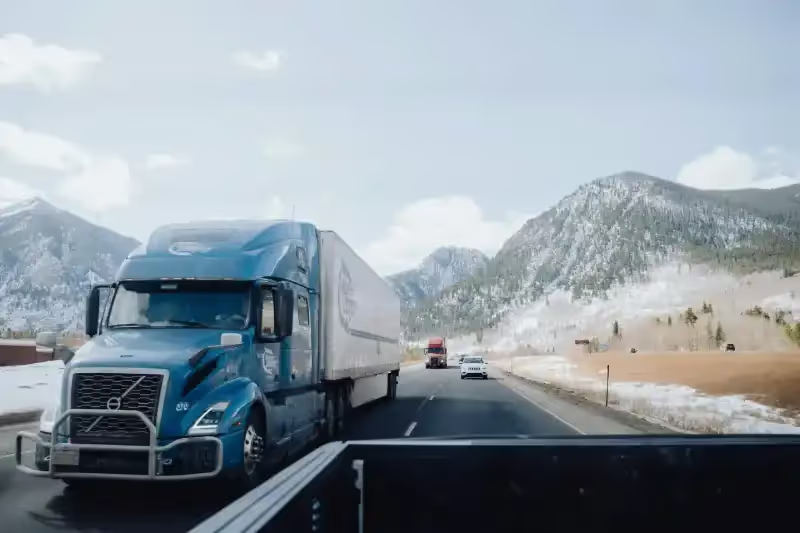
Understanding Trailer Electrical Issues
Trailer electrical issues like dim lights, dead power, or faulty brakes stem from bad grounds, wiring damage, or blown fuses. Regular checks prevent failures on the road.
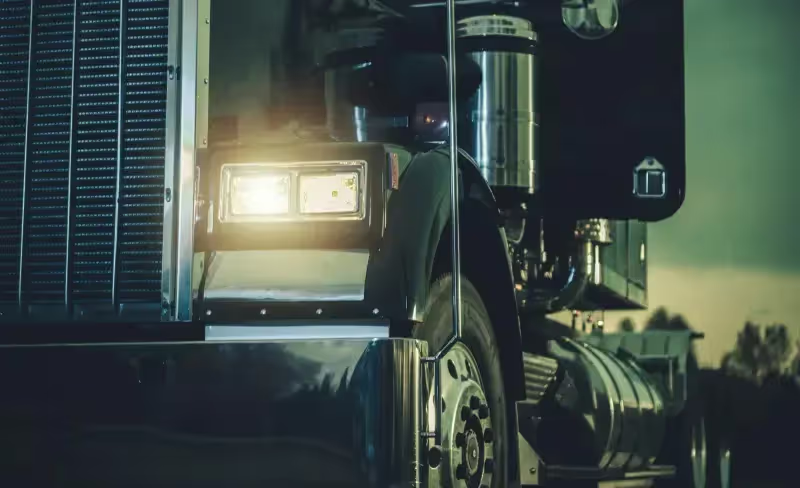
Common Brake Problems in Heavy-Duty Trucks and How to Fix Them
Heavy-duty truck brakes require vigilance. Common issues include air leaks, overheating, and slack adjuster failure. Address early signs like pulling or unusual noises to avoid costly repairs. Regular inspections, component replacements, and prompt fixes ensure safety and optimal performance.

Analytics for Optimal Fleet Management
Fleet analytics optimize fleet operations by transforming raw data into actionable insights. Track metrics like fuel efficiency, maintenance schedules, and driver behavior to reduce costs, improve safety, and extend vehicle lifespan. Implement telematics for real-time data integration and maximize fleet performance.